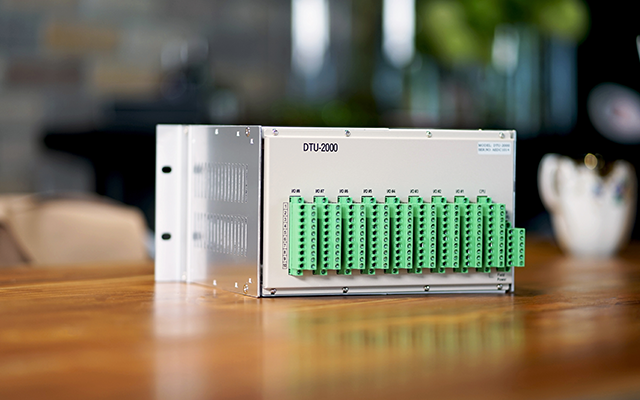
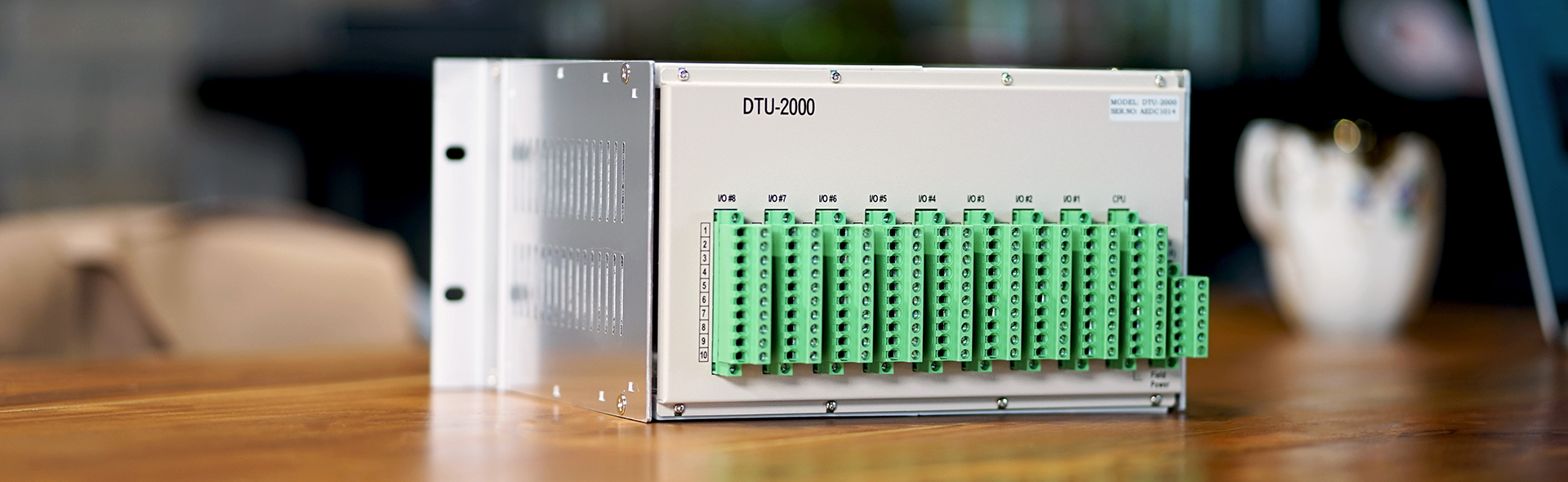
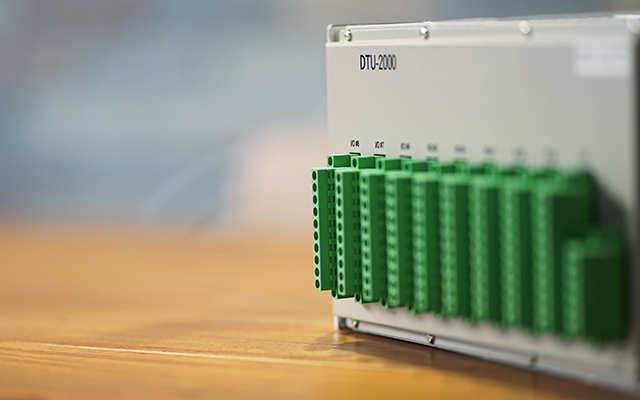
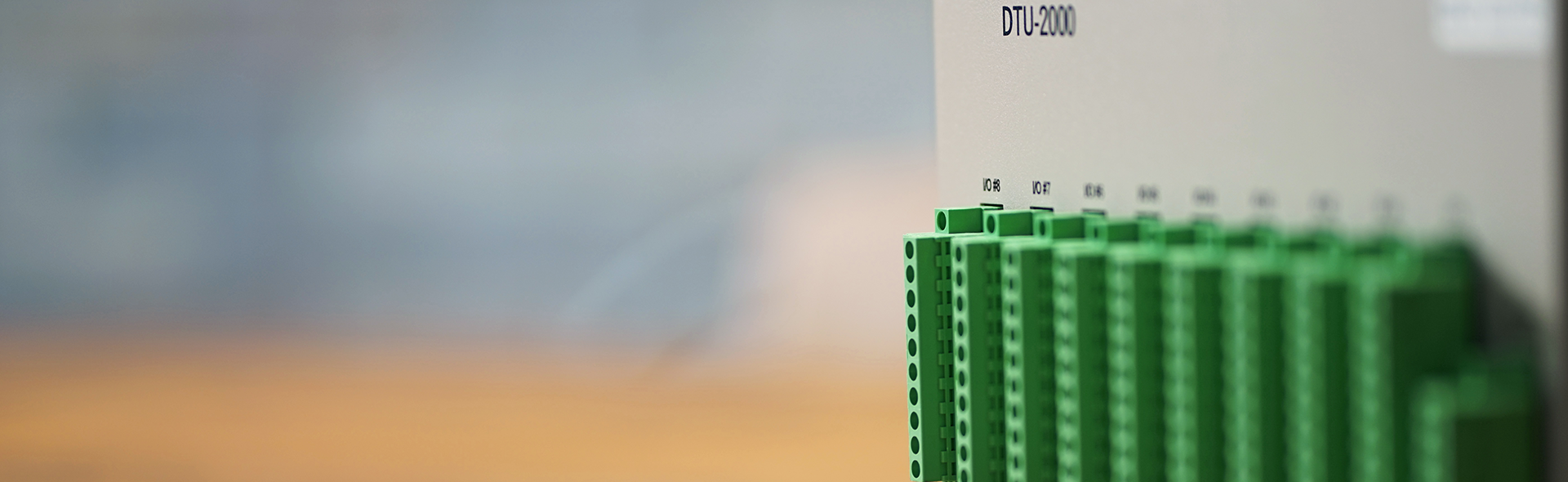
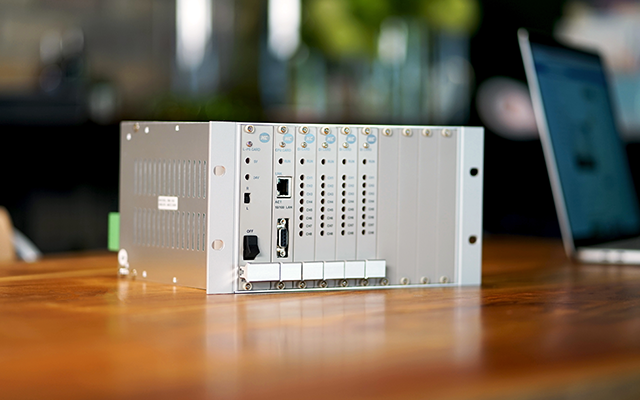
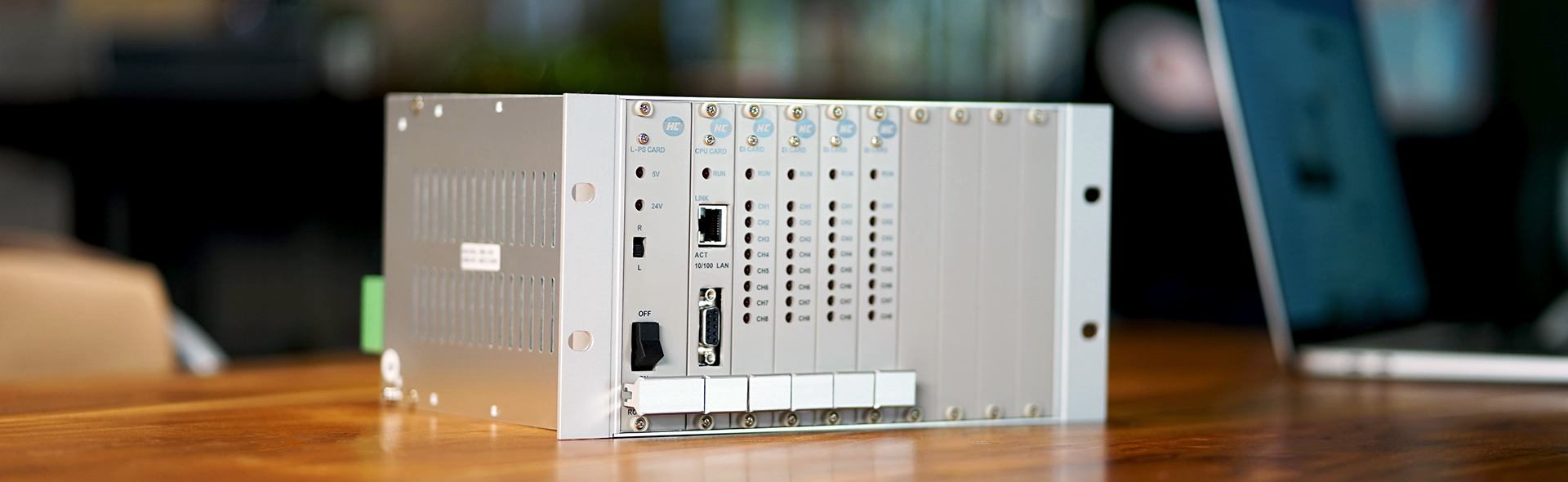
When DTU-2000 expands from small system to large or complex system, the existing cards and modules do not become obsolete. The DTU-2000 series can serve as communication server or the IED as below :IED
To use DTU as the IED equipment, there are two independent communication channels are provided by DTU CPU Card. One links to the host computer and the other one links to the power meter or IEDs for obtaining I/O information for such equipment and also transferring the output control command. Furthermore, the DTU also provides with I/O cards (AI, DI, AO, DOH and more) to collect the field information and to carry out the output of control command.
DTU-2000 series (Distribution Terminal Unit) is a distributive data acquisition and control system based on microprocessor. In common SCADA (Supervisory Control and Data Acquisition) system, DTU performs the tasks of collecting and processing of station data for both analog and digital signals; then DTU-2000 receives the command from host in master station and transmit back the acquired data, also to perform the function“check before execution” for station facilities to ensure a safe and reliable execution in system control.
DTU-2000 series is generally installed at on-site power stations to apply the monitor and control of signal performance.
DTU-2000 series is designed in multiple processor technique.
Each I/O Card has its own processor that is responsible for the basic data acquisition function.
The basic functions are as follows.
Features
- A. Data Acquisition Processing
- DTU acquires digital and analog signal from station plus processing and storage in the memory and ready to transmit the data back to communication server or control center.
- B. Sequence of Event Report
- DTU provides the SOE function (Sequence of Event) to monitor the status and sequence, or any changes of equipments at the station. An event is defined as a single change of state. Each time an event is detected, RTU will time tag the event and save a description of the event and the time tag in a first in first out (FIFO) butter. There is 1024 events butter in DTU.
- C. Control Output
- Two types of control command can be transmitted from the Master Station to devices in the power system via the DTU. One is Trip / Close command, the other is Direct Set point command.
- There are two types of control output using
- Trip/Close command. One is ON / OFF operation output to control CBs, ABSs and the other is
- Regulation operation output (raise / lower) to control the position of transformer taps.
- Two types of Trip / Close commands are supported.
- D. Communication Function
- The communication function of DTU can be divided into internal communication and external communication.
- SCADA Master: CDC Type II, DNP3.0, IEC870-5,
- CDT (China).
- DTU Sub-Master: ModBus RTU, DNP3.0, IEC870-5.
- IED : ModBus RTU, DNP3.0.
- E. Self-diagnostic Function
- DTU is designed with self-diagnostic function. Every abnormal status of DTU is recorded as System Event, or indicated by LED excitation on the panel.
- The System Event record can be retrieved by test set and store in its hard disk, which is very easy to detect errors in maintenance.
- F. Programmable Algorithm Function
- DTU has the capability of user definable “Sequential Algorithm”. The “Sequential Algorithm” within DTU can communicate through a common variable database which consists of analog inputs, digital inputs, accumula tor inputs, pseudo points, alarm (system) status, digital output, and system clock.
Accuracy
- Hardware Structure
- DTU hardware structure is designed as a plug-in type set up in a 19” rack. The plug-in type configuration is ideal for maintenance and expansion. The dimension of the card is followed by the European standard of 100mm × 160mm. DTU is consists of 4 Units.
- Power Supply Unit
- The power supply of DTU contains the following cards :
- L-PS Card : Power supply card comes in DC 18V - 40V Input and DC 5V (10W), DC 24V (3W) output; connects the back plane with 48-pin DIN connector that supplies 5V working power for the DTU and 24V driving power for DOH card.
- H-PS Card : Power supply card comes in AC 85V-265V or DC 65V - 375V input and DC 5V (10W), DC 24V (3W) output; connects the backplane with 48-pin DIN that supplies 5V working power for the DTU and 24V driving power for DOH Card.
- Main Unit
- The main unit of DTU consists of 1 backplane and 1 Master CPU card.
- Backplane :
- Backplane acts as buffer to the path of power supply and communication bus and with plugging slots for all circuit cards. Backplane consists of one power slot, one CPU slot and several I/O slots. Backplane is designed as pluggable type terminal for external wire connection.
- CPU Card :
- Uses 16-bit high speed microprocessor, with one Ethernet LAN port (RC-717 only) or one isolated RS-232/485 ports for host communication, one RS-232/485 port for power meter or IEDs, one RS-485 port for local IO communication, and one isolated RS232 port for Test Set.
- I/O Interface Unit
- DTU provides various types of I/O interface cards, which corresponds to the system requirements in a station. I/O card is able to devide into different functions of input and output which is to monitor and to study the status of operation in stations.
- The detailed description is listed as below :
- DI Card : Digital Input Card, 8 Points / Card. I/P : 8 channels at DC 24V, 48V, or 125V.
- ACC Card : Accumulator Card, 8 Points / Card for 2-wire input; 4 Points / Card for 3-wire input.
- I/P : 4 / 8 channels at DC : 24V, 48V, or 125V.
- DO Card : Unlatch Digital Output Card, 8 Points / Card. O/P : 8 channels
- DOH Card : Unlatch Digital Output Card, 4 Points + 1. O/P : 4 channels with1 Main Execution.
- ME (Main Execution) / Card.
- AI Card : Analog Input Card, 4 Differential Channels / Card, 1 sec Scan Time.
- I/P : ±1mA, 4 channels; I/P : 4-20 mA, 4 channels; or I/P: 5V, 4 channels.
- AO Card : Analog Output Card, 4 Different Channels / Card. I/P : ±1mA, 4 channels; or I/P: 4-20 mA, 4 channels.